UN Sustainable Development Goals
Ensure sustainable consumption and production patterns
Pavan Manvi holds up a small tube made from white textile, strong and yet elastic. The resistance is so great that he needs both hands to stretch it. “This material has just the right elasticity for a compression stocking,” he says, satisfied. As a researcher from the Institute of Textile Technology at RWTH Aachen University, Manvi knows that a perfect result is by no means a given. That’s because he and his colleagues have adopted an innovative new manufacturing approach: The fibers of the prototype are made partly from a molecule present in the air all around us that is reputed to play a major role in global warming – the greenhouse gas carbon dioxide, or CO2.
Now CO2 has turned a researcher’s dream into reality: It can replace a certain amount of crude oil, the scarce resource used predominantly as a raw material by the chemical and plastics industry to date. Both CO2 and crude oil contain carbon – a valuable element that is required for so many products, including textiles.
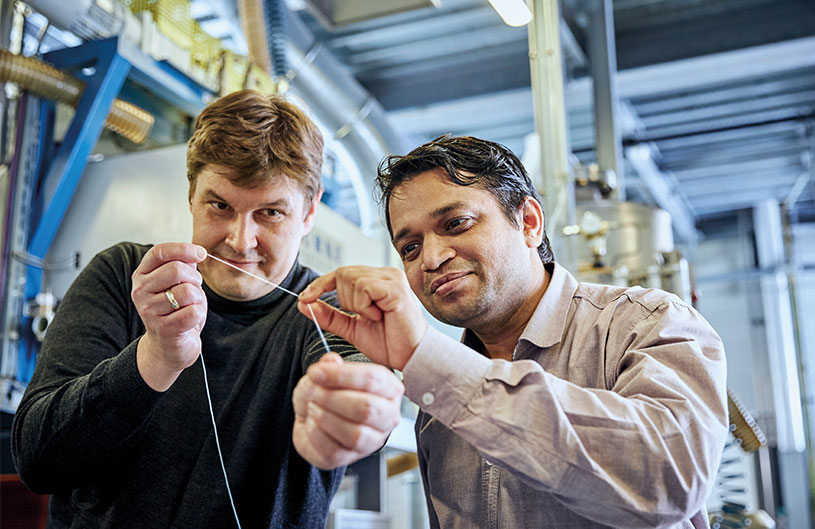
Tangible success: scientist Pavan Manvi from RWTH Aachen University (right) and Covestro researcher Dr. Jochen Norwig holding a synthetic fiber prototype made from CO2.
Synthetic fibers made from CO2
Manvi is making the most of this opportunity: He and his colleagues in Aachen, working alongside researchers from the Technical University of Berlin and Covestro, have succeeded in manufacturing market-ready synthetic fibers from CO2 and incorporating them in articles of clothing.
“We’ve demonstrated that we can produce high-performance fibers from thermoplastic polyurethane on a large scale in our melt spinning facility. This saves on fossil raw materials and reduces our CO2 footprint compared with conventional synthetic fibers,” says Manvi, who has been pursuing the research project at RWTH for the past three years. “We can also eliminate the solvents commonly used in the process and thus improve our environmental footprint even more.”
We can produce high-performance fibers using CO2
Pavan Manvi, Institute of Textile Technology, RWTH Aachen University
Saving fossil resources
At the heart of this is a pioneering process developed by Covestro and its partners. For the first time, up to 20 percent of the crude oil commonly used in the manufacture of polyol, a precursor of polyurethanes, can be replaced with CO2. This is difficult, since carbon dioxide is extremely inert and a great deal of energy is required to produce chemical reactions with it. However, Covestro helped develop a special catalyst that limits the amount of energy needed. “Thanks to this research breakthrough, we can now manufacture polyols based on CO2 on an industrial scale,” says Dr. Christoph Gürtler, who heads the catalyst research team at Covestro.
The innovative precursor known as cardyon® was initially devised for use in the flexible polyurethane foam required to make mattresses and upholstered furniture – products with this innovative foam are already available on the market. However, cardyon® recently also made a name for itself in the world of sports when it was used for the new synthetic surface of a well-known hockey club in Krefeld (see “Fit with CO2”).
Next step in the use of carbon dioxide
Fit with CO2
It’s a world‘s first: synthetic sports flooring manufactured using CO2. The world’s first surface of this kind has been in use at a hockey club in Krefeld, Germany since 2018, now that Covestro has developed a new CO2-based binder for it. Flexible foam manufactured from carbon dioxide has already been on the market for some time.
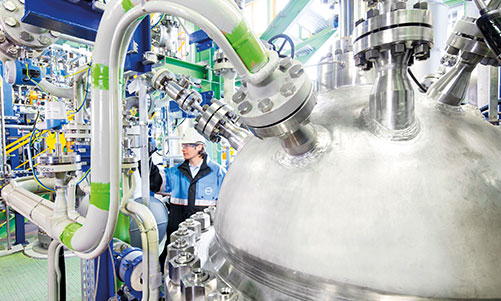
1. Production: Covestro manufactures the first binder made from carbon dioxide in Dormagen near Cologne.
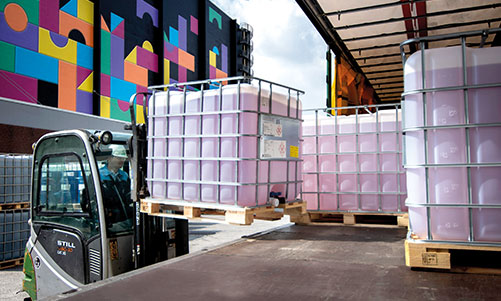
2. Delivery: The innovative precursor is supplied to the first customer, sports flooring producer Polytan.
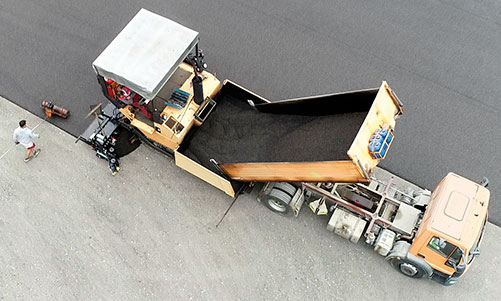
3. Construction: Polytan lays an elastic underfloor made of rubber granulate and a CO2-based binder on a hockey pitch in Krefeld.
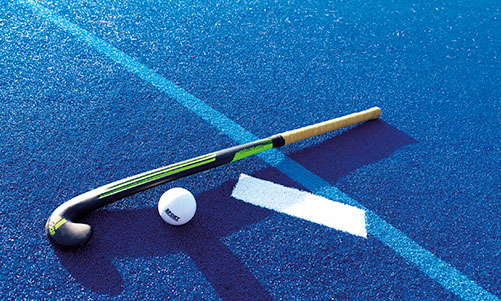
4. World’s first: The new, bright blue artificial pitch at the “Crefelder Hockey and Tennis Club” is a big attraction – it’s great to play on and is particularly eco-friendly.
Fit with CO2
Tested by textile manufacturers
Now the textile industry will become an application area for cardyon®. Its elastic fibers have already been tested by companies and used in the manufacture of yarns, socks, compression stockings and tapes. Textile manufacturers insist that the new material must be of the same quality in every respect and enable processing just as easily as conventional fibers. “We want to run tests to see how the new technology can be harnessed across various stages of the value chain,” says the chemist Dr. Jochen Norwig, who is responsible for coordinating an EU-funded research project at Covestro that includes the development of the new CO2 fibers.
And Covestro has its sights on even more application areas. “CO2 is increasingly becoming an all-purpose raw material,” says catalyst expert Gürtler, whose view coincides with that of other professionals from the worlds of science, politics and society at large (see “Moving away from oil”). “We’re setting our sights on many other applications and sectors besides synthetic fibers and the textile industry. For instance, our researchers are working on the use of carbon dioxide in the production of car seats and in insulating materials for buildings and refrigerators.”
Cross-industry collaboration
Gürtler and his colleagues are particularly fascinated by broad cross-industry approaches such as that of the pan-European research project “Carbon4PUR”. Here, Covestro is heading a team of 14 partners from seven countries who are exploring how to extract the carbon from steel industry emissions, such as CO2 and carbon monoxide, for use in chemical processes instead of the crude oil used to date. “Ultimately our aim is to incorporate CO2 in many other types of plastic and to use it to replace as many fossil materials as we can,” says Gürtler. The goal is to deploy carbon as intelligently as possible in order to close the carbon cycle.
Raw Materials Summit 2018
Moving away from oil
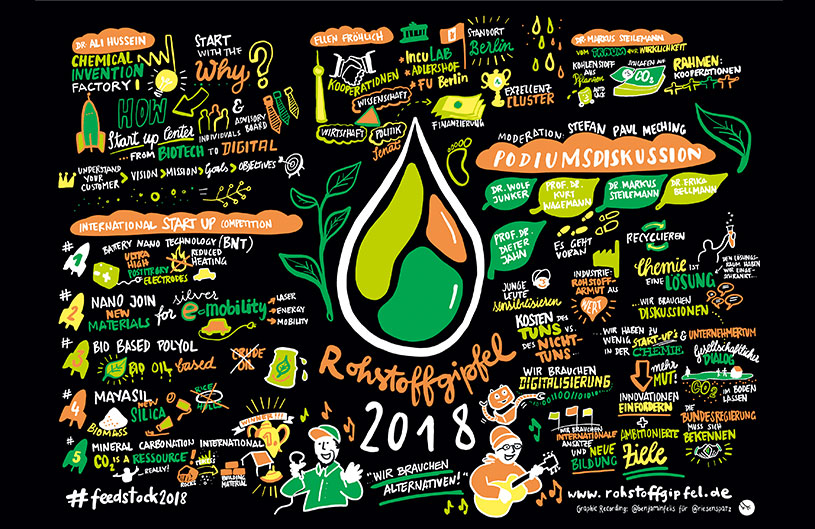
“We need alternatives” – the Raw Material Summit 2018 in Berlin, which Covestro helped organize, as seen by a cartoonist.
Strong partners, special skills and various perspectives are key to mastering difficult challenges. At least, that’s the opinion of the Technical University of Berlin, the German Society for Chemical Engineering and Biotechnology (DECHEMA) and Covestro, who extended a joint invitation to the 2018 Raw Materials Summit on the university’s premises. The event saw renowned representatives from the worlds of business and science, politics and society come together to shed light on a complex challenge: how can more energy and resources be saved in chemical production to aid the cause of climate protection? How worthwhile is the use of sustainable resources derived from plants and CO2 in order to reduce our dependency on fossil fuels such as crude oil? How far can and should we go?
The speakers, among them by Dr. Erika Bellmann, Senior Policy Advisor at WWF Germany, had clear messages: “We triggered the climate crisis and are responsible for perpetuating it with our focus on coal, gas and oil. So we need to move away from fossil raw materials and towards new ones.” The conditions for this are favorable: The European Union is supporting a number of projects in this regard, and the German government has also committed itself to change when it comes to raw materials.
We support the search for substitutes for fossil raw materials.
Dr. Georg Schütte, State Secretary in the Federal Ministry of Education and Research, Germany
“Innovative technologies already make it possible to produce the sustainable chemicals and fuels of the future,” said Dr. Georg Schütte, State Secretary in the Federal Ministry of Education and Research, which sponsored the Raw Materials Summit. “We support the search for substitutes for fossil raw materials through targeted research funding in the field of bioeconomics and the use of CO2. This is also how we safeguard our international competitiveness.”
The summit hopes for inspiration from young companies in particular. It sends a signal for a more entrepreneurial spirit with an international ideas competition that saw five start-ups from three continents selected as “Resource Innovators 2018”. The first prize went to the Australian company Mineral Carbonation International, which produces building materials and other valuable industrial products from CO2.
You will find more information on CO2 on the website of the Technical University of Berlin.